What is Porosity in Welding: Finest Practices for Staying Clear Of Porous Welds
What is Porosity in Welding: Finest Practices for Staying Clear Of Porous Welds
Blog Article
Understanding Porosity in Welding: Discovering Reasons, Impacts, and Prevention Methods
As professionals in the welding sector are well conscious, understanding the reasons, results, and prevention techniques connected to porosity is important for attaining durable and reliable welds. By delving into the origin creates of porosity, examining its damaging effects on weld quality, and checking out effective avoidance strategies, welders can enhance their expertise and skills to generate premium welds regularly.
Typical Reasons of Porosity
Porosity in welding is largely triggered by a mix of aspects such as contamination, incorrect shielding, and insufficient gas insurance coverage during the welding process. Contamination, in the kind of dust, oil, or rust on the welding surface, produces gas pockets when warmed, leading to porosity in the weld. Inappropriate shielding occurs when the shielding gas, generally used in procedures like MIG and TIG welding, is not able to completely protect the liquified weld swimming pool from responding with the surrounding air, causing gas entrapment and subsequent porosity. Additionally, insufficient gas protection, commonly due to inaccurate flow prices or nozzle positioning, can leave components of the weld vulnerable, enabling porosity to form. These aspects collectively add to the development of gaps within the weld, compromising its honesty and potentially causing architectural problems. Comprehending and attending to these common reasons are important steps in stopping porosity and making certain the top quality and toughness of welded joints.
Results on Weld Quality
The existence of porosity in a weld can considerably endanger the overall quality and honesty of the bonded joint. Porosity within a weld produces gaps or tooth cavities that deteriorate the framework, making it more vulnerable to breaking, rust, and mechanical failing.
Additionally, porosity can impede the efficiency of non-destructive testing (NDT) techniques, making it challenging to find other defects or gaps within the weld. This can result in significant safety problems, especially in important applications where the structural honesty of the bonded components is paramount.

Prevention Techniques Introduction
Offered the detrimental effect of porosity on weld top quality, efficient avoidance methods are crucial to maintaining the structural integrity of bonded joints. One of the key prevention methods is extensive cleaning of the base products prior to welding. Contaminants such as oil, oil, corrosion, and dampness can add to porosity, so making sure a clean work surface area is essential. Proper storage space of welding consumables in completely dry conditions is likewise critical to avoid dampness absorption, which can bring about gas entrapment throughout welding. In addition, selecting the proper welding specifications, such as voltage, existing, and take a trip speed, can assist decrease the risk of porosity formation. Ensuring adequate shielding gas circulation and insurance coverage is another vital prevention method, as insufficient gas protection can cause climatic contamination and porosity. Proper welder training and accreditation are vital for executing preventive measures effectively and regularly. By incorporating these avoidance techniques right into welding practices, the event of porosity can be dramatically decreased, causing more powerful and a lot more trustworthy bonded joints.
Importance of Correct Shielding
Correct shielding in welding plays a vital duty in preventing atmospheric contamination browse this site and guaranteeing the honesty of bonded joints. Shielding gases, such as argon, helium, or a blend of both, are generally used to protect the weld pool from responding with aspects in the air like oxygen and nitrogen. When these responsive elements enter into contact with the hot weld pool, they can cause porosity, causing weak welds with reduced mechanical buildings.
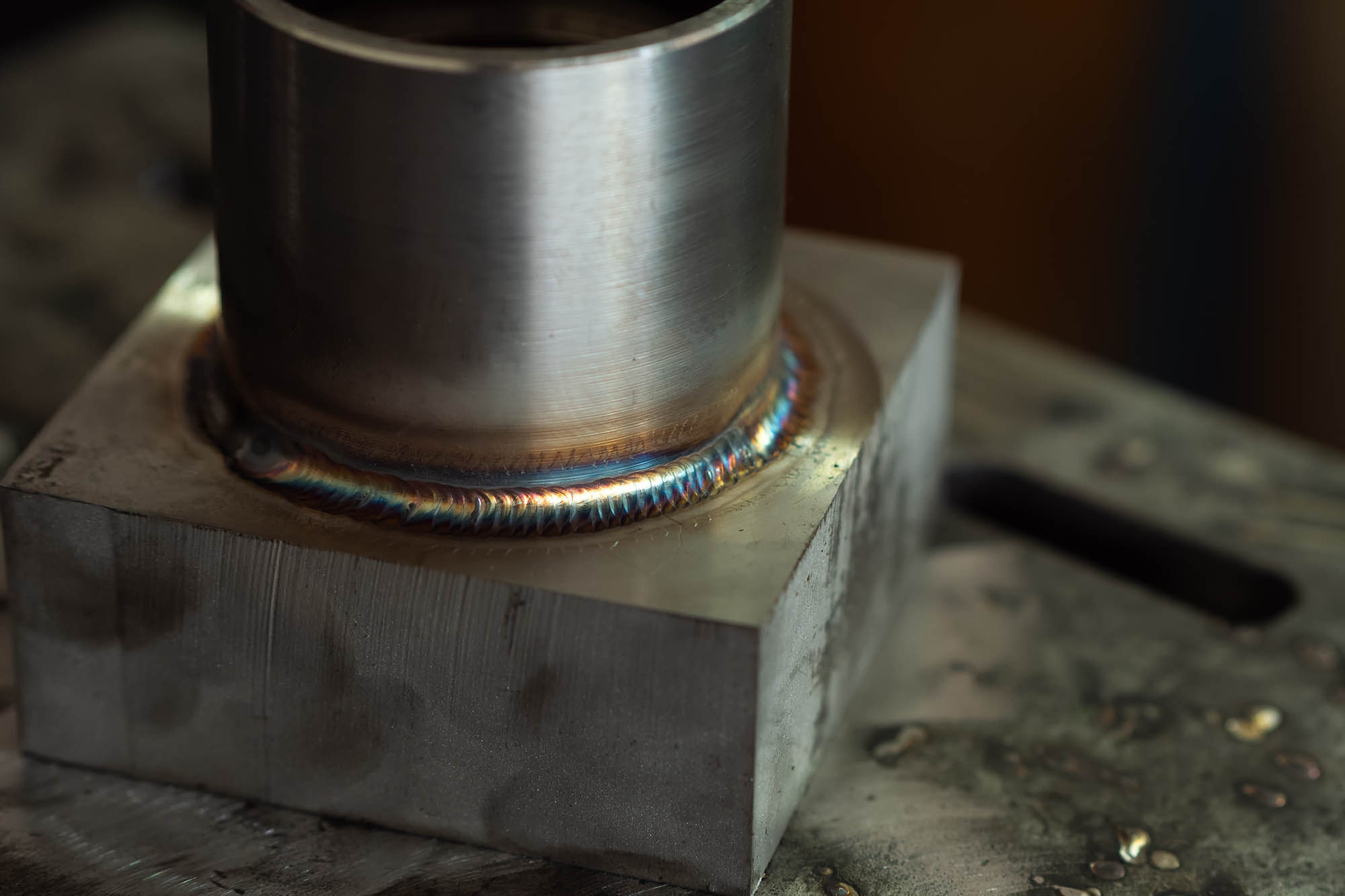
Insufficient securing can cause different problems like porosity, spatter, and oxidation, compromising the architectural integrity of the bonded joint. Adhering to proper securing techniques is necessary to produce premium welds with minimal flaws and guarantee the long life and integrity of the welded elements.
Surveillance and Control Techniques
Just how can welders successfully keep track of and control the welding process to make sure optimum results and protect against flaws like porosity? One key technique is via using advanced monitoring technologies. These can include real-time tracking systems that offer comments on specifications such as voltage, current, travel speed, and gas flow prices. By continually keeping track of these variables, welders can recognize discrepancies from the ideal conditions and make immediate modifications to browse this site stop porosity formation.

In addition, executing appropriate training programs for welders is crucial for keeping track of and managing the welding process properly. What is Porosity. Educating welders on the significance of preserving constant criteria, such as proper gas protecting and travel rate, can assist protect against porosity problems. Regular evaluations and qualifications can likewise ensure that welders are competent in tracking and regulating welding processes
Additionally, using automated welding systems can improve monitoring and control capacities. These systems can precisely manage welding parameters, lowering the possibility of human mistake and making certain consistent weld quality. By integrating innovative tracking innovations, training programs, and automated systems, welders can successfully keep an eye on and manage the welding process to decrease porosity defects and attain top notch welds.
Final Thought
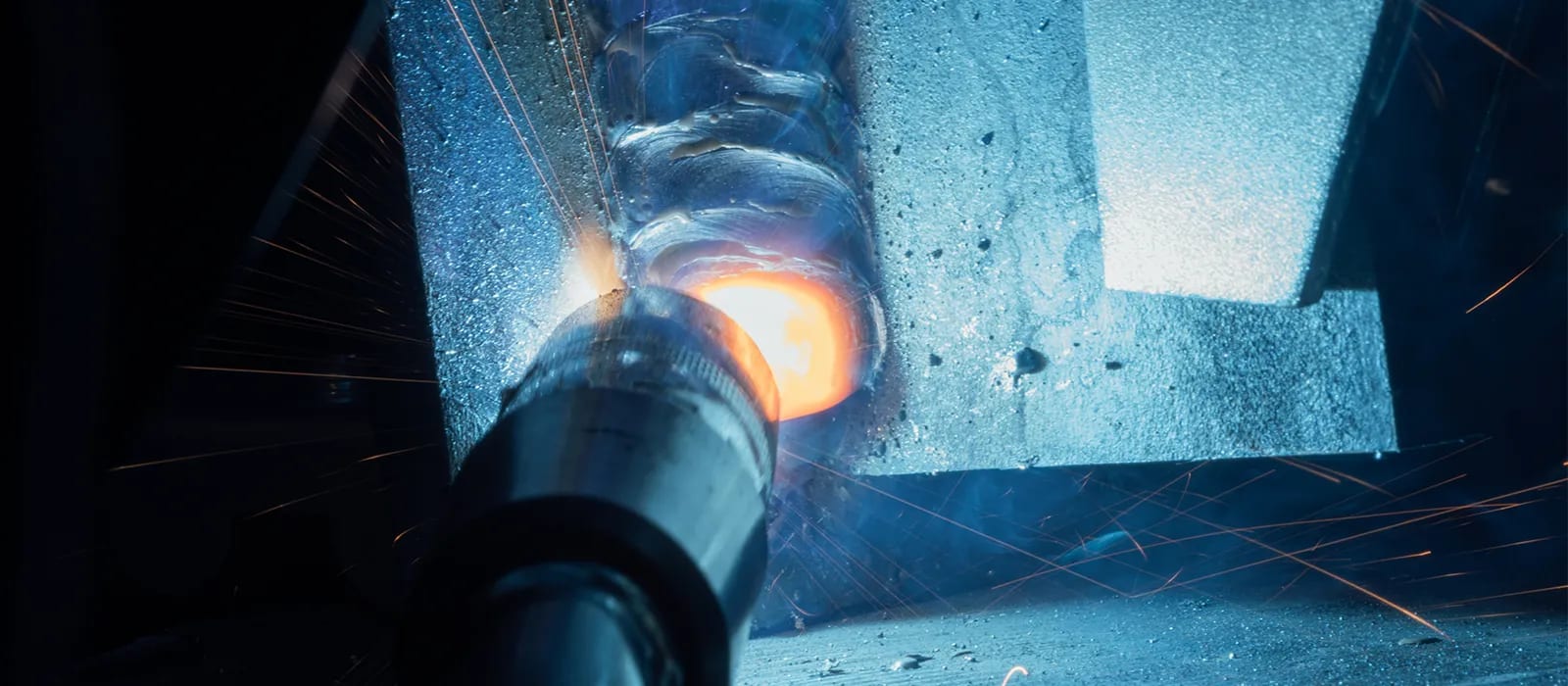
Report this page